Are you familiar with the term “4 Way Inspection”? If not, you’ve come to the right place! In this in-depth guide, we’ll delve into the world of 4 Way Inspection and explore its significance within the construction industry.
From understanding the definition and purpose to exploring its importance, we’ll leave no stone unturned. So, whether you’re a seasoned construction professional or an aspiring homeowner looking to ensure a seamless construction process, this guide has you covered.
First and foremost, let’s clarify what exactly a 4 Way Inspection entails. To put it simply, it’s an all-encompassing inspection process that evaluates four main areas of a construction project: electrical, plumbing, mechanical, and structural.
By conducting this thorough examination, construction professionals can identify potential issues or discrepancies, paving the way for a successful and safe project completion.
Now, you might be wondering why 4 Way Inspection holds such immense importance in the construction industry. Well, the answer lies in the critical role it plays in ensuring compliance with building codes, maximizing efficiency, and minimizing future complications.
By thoroughly assessing the electrical, plumbing, mechanical, and structural components, construction projects can proceed smoothly, avoiding costly rework and potential hazards.
Throughout this guide, we’ll thoroughly explore each facet of the 4 Way Inspection process, shedding light on its significance and the intricacies involved in assessing each area.
We’ll discuss the specific details that make up each inspection, common issues that arise, and offer valuable tips to help you navigate the inspection process seamlessly.
By the end, you’ll possess a comprehensive understanding of 4 Way Inspection and be better equipped to ensure the success of your future construction projects.
So, let’s dive right in and discover the ins and outs of 4 Way Inspection for a world of construction excellence!
Table of Contents
New Construction

In the context of newly constructed buildings, a 4 Way Inspection refers to a comprehensive examination and evaluation of various systems before the final handover and occupancy.
It is an essential step to ensure that all aspects of the construction meet industry standards and best practices, and that the building is safe for occupancy.
Importance of Comprehensive Examination
During new construction, it is crucial to conduct a thorough inspection of the building to identify any potential issues or deficiencies in the various systems. This includes plumbing, walls, framing, electrical, and more.
A comprehensive examination helps ensure that all systems are properly installed, compliant with necessary codes and regulations, and functioning as intended.
Read More on What is Site Inspection? All You Need to Know
Examination and Evaluation of Various Systems
The 4 Way Inspection involves a detailed assessment of each system present in the building to ensure its proper functioning. Let’s take a look at some of the key systems that are typically examined:
- Plumbing: The plumbing system is thoroughly inspected to check for any leaks, proper installation of pipes, functioning of fixtures, and compliance with plumbing codes.
- Walls: The walls are examined to ensure proper insulation, structural integrity, and compliance with building codes.
- Framing: The structural framing of the building is inspected to guarantee stability, proper construction techniques, and adherence to building codes.
- Scheduled Inspections: Throughout the construction process, scheduled inspections are conducted to ensure that every stage meets the necessary standards.
- Required Compliance: The building must comply with all applicable local, state, and national codes, regulations, and ordinances.
- Rough Inspection: A rough inspection is conducted to check the installation of electrical, plumbing, and mechanical systems before they are concealed by finishes.
- Site Inspection: The overall site is evaluated for compliance with environmental regulations, drainage systems, and construction permits.
- Electrical Inspection: Electrical systems, wiring, and fixtures are inspected to ensure proper installation, grounding, and compliance with electrical codes.
- Documentation: Detailed documentation is created throughout the inspection process to record findings, non-compliances, and necessary corrective actions.
- Safety: The safety of the building, including fire safety measures, emergency exits, and proper ventilation, is thoroughly assessed.
- Handover and Occupancy: Once the 4 Way Inspection is successfully completed and any necessary corrective actions are taken, the building is deemed safe for occupancy.
- Industry Standards and Best Practices: The 4 Way Inspection ensures that the new construction project aligns with industry standards and follows best practices in all aspects.
Read More on Container Pools Brisbane – Discover the Brilliance
Inspection
When it comes to construction projects, inspections play a crucial role in ensuring quality and safety. One type of inspection that is commonly conducted is the 4 Way Inspection. Let’s delve deeper into this essential part of the inspection process.
A. The Concept of 4 Way Inspection as an Essential Part of the Inspection Process
The 4 Way Inspection is a comprehensive examination conducted at different stages of construction. It involves assessing the quality and safety of the construction to ensure compliance with building codes and regulations.
This type of inspection is crucial in identifying any issues or potential risks before proceeding to the next phase of construction.
B. Different Stages of Construction Where Inspections Occur
During the 4 Way Inspection, specific stages of construction are targeted for examination. These stages include the foundation, framing, rough-in, and final walkthrough. Inspections at each of these stages allow for a thorough assessment of the construction’s integrity, ensuring that all necessary requirements are met.
C. Verification of Quality and Safety of the Construction
One of the primary objectives of the 4 Way Inspection is the verification of both the quality and safety of the construction. Inspectors meticulously examine every aspect of the project to identify any deficiencies, structural weaknesses, or safety hazards.
By doing so, they ensure that the construction meets industry standards and best practices, providing peace of mind to both the builder and future occupants.
Overall, the 4 Way Inspection is a vital part of the inspection process. Through thorough examination and analysis, it helps maintain the highest standards of quality and safety in construction projects.
- Completely revised 9th Edition of Code Check.
- Easy-to-use guide to building codes for a safe and sound home.
- Shows you how to build a safe, sound house without a professional inspector.
- Incorporates the most current building codes from the International Residential Code (IRC).
- Provides hundreds of illustrations in full-color.
- Details the correct installation of critical items.
- Answers common building code questions from today’s do-it-yourselfer.
Read More on How to Adhere to Legal Weight Limits for 40′ Shipping Container
Plumbing in 4 Way Inspection
During a 4 Way Inspection, the role of plumbing systems is crucial in ensuring the functionality and efficiency of a newly constructed property. These systems play a significant part in providing clean water supply and proper drainage.
A. Role of Plumbing Systems in 4 Way Inspection
Plumbing systems are responsible for the delivery of fresh water to various fixtures such as faucets, showers, and toilets throughout the building. Additionally, they are instrumental in removing wastewater and other waste materials from the property.
Plumbing systems consist of a network of pipes, valves, and fixtures that work together to ensure a continuous flow of water throughout the property. During a 4 Way Inspection, the functionality and compatibility of these systems are thoroughly examined and evaluated.
B. Examination and Evaluation of Plumbing Systems During the Inspection Process
Qualified inspectors carefully examine all aspects of the plumbing systems to ensure their proper installation and functionality. They inspect the main water supply lines, drain lines, water heaters, and individual fixtures to identify any potential issues.
The inspection includes checking for leaks, blockages, proper water pressure, and adequate drainage. Inspectors also verify the correct installation of plumbing fixtures and the adherence to industry standards.
Read More on 20′ Container Legal Weight for Safe and Efficient Transportation
C. Ensuring Compliance With Plumbing Codes and Regulations
During the 4 Way Inspection, one of the primary objectives is to ensure compliance with local plumbing codes and regulations. These codes are in place to ensure the safety and well-being of occupants, as well as to maintain proper sanitation standards.
Inspectors thoroughly examine the plumbing systems to ensure that they meet these codes. They pay close attention to pipe materials, venting systems, backflow prevention devices, and septic systems where applicable. Non-compliance with these regulations may result in significant issues later on.
The plumbing aspect of a 4 Way Inspection requires the expertise of trained professionals who understand the intricacies of the systems. Engaging a qualified plumbing inspector is essential to identify any potential issues and ensure a smooth completion of the inspection process.
Read More on Are Shipping Container Homes Legal In Georgia? Find Out Why
What is 4 Way Inspection: Part 5 – Walls
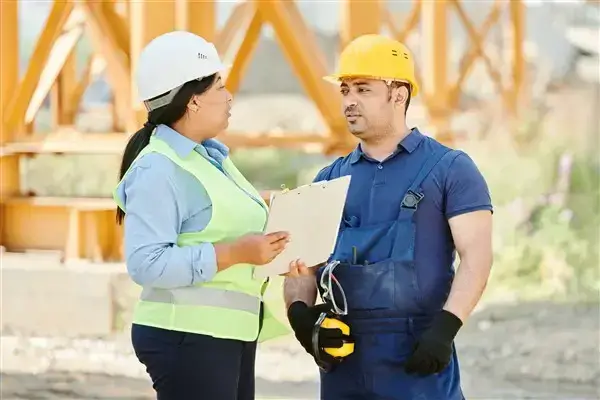
Analysis of the Role of Walls in 4 Way Inspection
When it comes to the 4 Way Inspection process, walls play a crucial role in ensuring the overall safety and structural integrity of a building.
Not only do walls provide the necessary support and division of space, but they also act as a barrier against external elements and offer privacy to the occupants. Therefore, a thorough analysis of the walls during the inspection is of utmost importance.
Inspection Requirements and Standards for Walls
During the 4 Way Inspection, specific requirements and standards need to be met for walls to ensure compliance with applicable building codes and regulations.
These include proper installation, adequate thickness, fire resistance, and meeting noise reduction standards. Walls should also be inspected for any signs of cracks, water damage, or deterioration that may compromise their structural integrity.
Identifying any Issues or Deficiencies Related to Walls During the Inspection Process
One of the key objectives of the 4 Way Inspection is to identify any issues or deficiencies related to walls that may pose a risk or hinder the functionality of the building.
This inspection process involves thorough examination of the walls for proper insulation, attachment, and finishing. Any signs of leaks, moisture, or mold growth should be promptly addressed to ensure a healthy living environment.
- Poor insulation: Insufficient insulation in the walls can lead to energy loss, increased utility bills, and discomfort for the occupants. It is crucial to check for proper insulation materials and installation during the 4 Way Inspection.
- Improper attachment: Walls need to be securely attached to the framework of the building to provide stability and resist external forces. The inspection should verify that the walls are adequately fastened and anchored.
- Inadequate finishing: The finishing of the walls, such as paint or wallpaper, should be inspected for any visible defects, unevenness, or peeling. Good quality finishes not only enhance the aesthetics of the space but also protect the walls from damage.
Identifying these issues or deficiencies during the 4 Way Inspection allows for timely repairs or modifications. This ensures that the walls meet the highest standards of quality and safety.
Read More on Easy Explanation To What Is A Plumbing Process
Framing
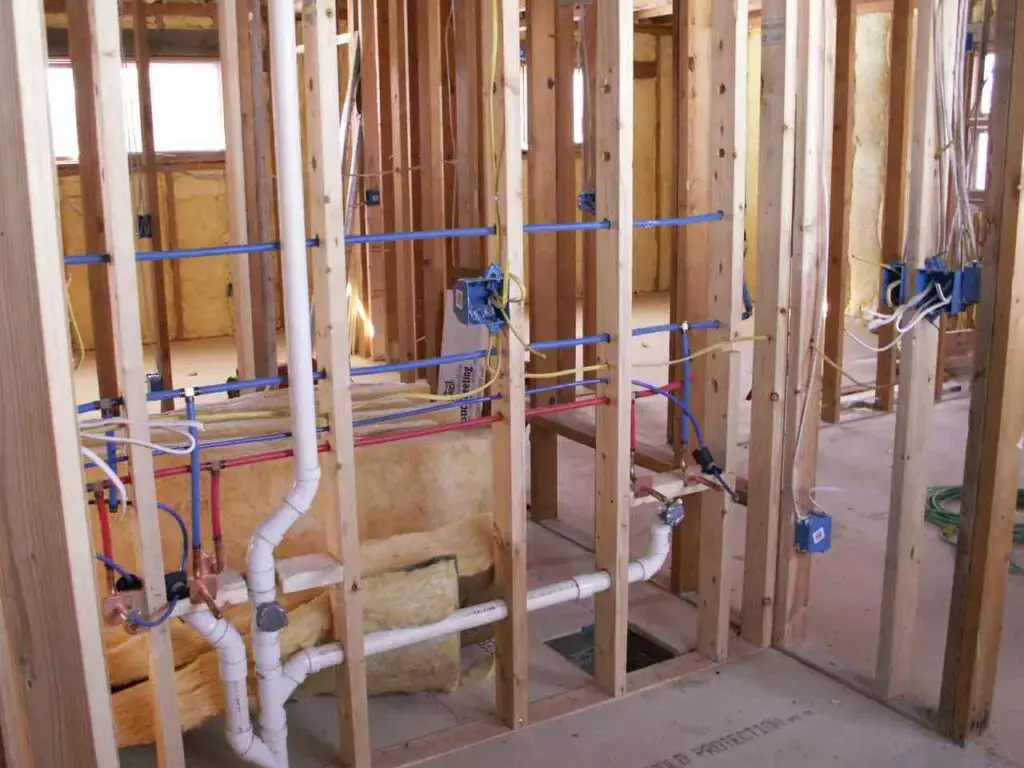
The framing stage is a crucial part of the 4 Way Inspection process in new construction projects. This stage involves the installation of the structural framework that will support the entire building. Proper framing ensures the stability, durability, and safety of the structure.
A. Significance of Framing in 4 Way Inspection
Framing plays a significant role in the overall 4 Way Inspection process. It not only supports the weight of the building but also determines its layout, size, and shape.
The framing phase is considered the backbone of the construction project, as it provides the framework on which all other components are built.
During the 4 Way Inspection, the framing is thoroughly examined to ensure that it meets the required standards and codes.
Any structural defects or issues in the framing can compromise the integrity of the entire building. Therefore, it is essential to pay close attention to detail during the framing stage.
B. Evaluation of Structural Integrity and Quality in Framing
One of the primary purposes of the 4 Way Inspection is to evaluate the structural integrity and quality of the framing.
Inspectors carefully examine the framing elements, including beams, columns, walls, and roof structures, to assess their strength, stability, and overall quality. Any signs of weakness or deficiencies are identified and addressed to prevent future problems or hazards.
Inspectors check for proper installation of framing components, ensuring that they are level, plumb, and straight. They evaluate the connections between framing elements. These include joints, fasteners, and supports, to ensure they are secure and can withstand the intended loads and forces.
Any deviations from the structural plans or deficiencies in the framing materials are noted and rectified before proceeding with the construction process.
Read More on How Do You Prevent Mold In Shipping Containers? Easy
C. Ensuring Compliance with Structural Codes and Best Practices
Another critical aspect of the framing stage in the 4 Way Inspection is ensuring compliance with structural codes and best practices.
Building codes provide a set of regulations and standards that must be followed to ensure the safety, stability, and durability of the structure. Inspectors ensure that the framing meets or exceeds these codes and follows industry best practices.
During the framing inspection, inspectors pay attention to key areas, such as load-bearing walls, floor systems, roof structures, and structural connections.
They verify that the framing components are properly spaced, adequately supported, and properly nailed or fastened. Inspectors also assess the size and stiffness of the framing members, ensuring that they are appropriate for the specific design and intended use of the building.
By ensuring compliance with structural codes and best practices, the 4 Way Inspection helps guarantee that the framing will provide a safe and structurally sound building for its occupants.
Scheduled Inspections
In the process of a 4 Way Inspection, scheduled inspections play a vital role in ensuring the smooth and successful completion of a construction project.
These inspections are carefully planned and carried out at specific stages of the construction process to ensure regulatory compliance and adherence to industry standards.
Importance of Scheduled Inspections in the 4 Way Inspection Process
Scheduled inspections are crucial because they allow construction projects to be thoroughly evaluated and verified for compliance with relevant codes and regulations.
By conducting inspections at different stages of construction, any potential issues or concerns can be identified and addressed early on, saving both time and resources.
These inspections also serve as an opportunity to ensure that the construction is in line with the approved plans and specifications. By examining the progress made in each stage, any deviations or inconsistencies can be detected and rectified promptly, preventing costly errors and rework.
Read More on How To Build A Container Home Step-by-Step For Beginners And Starters
Ensuring the Timely Completion of Inspections at Different Stages of Construction
Timely completion of scheduled inspections is essential for the smooth progression of a construction project. Each stage of the construction process has specific milestones that need to be met. And inspections act as checkpoints to assess whether these milestones have been achieved.
By adhering to a structured inspection schedule, construction managers can effectively plan and allocate resources to ensure that inspections are carried out promptly. This helps in preventing delays and keeps the construction project on track, ultimately leading to its timely completion.
Benefits of Adhering to a Structured Inspection Schedule
Adhering to a structured inspection schedule offers numerous benefits to both construction teams and clients. Firstly, it provides accountability and transparency throughout the construction process. Clients can have confidence knowing that their project is being thoroughly inspected and monitored at every stage.
Secondly, a structured inspection schedule helps in minimizing defects and deficiencies. By catching and addressing issues early on, the need for costly rework and repairs is significantly reduced, saving both time and money.
Lastly, adhering to a structured inspection schedule ensures that the construction project meets all necessary regulations and standards. This reduces the risk of non-compliance issues and potential legal consequences.
In conclusion, scheduled inspections are a crucial component of the 4 Way Inspection process. They allow for thorough evaluation, timely completion of inspections, and numerous benefits in terms of compliance, accountability, and cost savings.
By following a structured inspection schedule, construction projects can achieve successful outcomes and deliver high-quality results.
Required Compliance
In a 4 Way Inspection, required compliance refers to adhering to building codes, regulations, and industry standards to ensure safety and meet legal obligations.
This step is crucial in the construction process as it helps ensure that the building or structure being constructed is in compliance with all necessary guidelines.
Demonstrating adherence to building codes, regulations, and industry standards is important for several reasons. Firstly, it helps guarantee that the construction project meets the required quality standards and specifications set by governing bodies.
This not only ensures the safety of those who will occupy the building but also protects the investment of the property owner.
Additionally, complying with building codes and regulations helps to avoid potential legal issues or fines that may arise from non-compliance. It is the responsibility of the construction team, including contractors and inspectors, to ensure that all work is done in accordance with the applicable laws and regulations.
By prioritizing required compliance in a 4 Way Inspection, construction professionals can demonstrate their commitment to delivering high-quality work that meets industry standards and best practices.
This not only enhances the reputation of the construction company but also instills confidence in the clients and occupants of the building.
Read More on Is It Cheaper To Build A Barndominium Or Container Home? Easy
Rough Inspection: Overview of the rough-in stage in 4 Way Inspection
During the progression of a new construction project, there are several key stages that require thorough inspections to ensure quality and safety.
One such stage is the rough-in inspection, which is an essential part of the 4 Way Inspection process. In this section, we will delve into the specifics of the rough inspection and its significance.
Purpose and Objectives of the Rough Inspection
The rough inspection serves as a critical checkpoint in the construction timeline. It is conducted after the completion of the plumbing, walls, and framing stages.
The primary purpose of this inspection is to meticulously examine the building’s essential components, such as plumbing systems, electrical wiring, ventilation, and any other elements that are concealed within the walls or floors.
By conducting the rough inspection, the construction team aims to ensure that all work completed thus far adheres to the required compliance standards and local building codes. Additionally, it allows the identification and rectification of any potential issues or deficiencies before proceeding to the next stages of construction.
Identifying and Addressing Any Issues or Deficiencies Before Proceeding
During the rough inspection, a qualified inspector thoroughly examines the various systems present in the building, assessing their condition and functionality. This includes inspecting the plumbing work to ensure proper installation and functionality of fixtures, pipes, and drains.
The inspector also checks the walls and verifies that they meet structural requirements and contain the necessary insulation.
Furthermore, the electrical system undergoes rigorous scrutiny to ensure proper wiring, grounding, and circuitry. Any issues or deficiencies in these critical areas are identified, documented, and brought to the attention of the construction team.
Addressing these issues promptly is essential to avoid future complications, possible structural damage, and potential hazards.
By conducting a thorough rough inspection, construction projects can progress smoothly, safeguarding the interests of both builders and future occupants. It is a crucial step towards ensuring that the upcoming stages of the project are executed efficiently and in compliance with industry standards and best practices.
Read More on Affordable Homes In Defuniak Springs
Site Inspection
A site inspection is a crucial part of the 4 Way Inspection process. It plays a significant role in ensuring the quality and compliance of a construction project. In this phase, inspectors carefully examine the site to identify any site-related issues and ensure the project meets all regulations and requirements.
Role of Site Inspections in 4 Way Inspection
Site inspections serve as a means of verifying that the construction project is being carried out according to the approved plans and specifications. Inspectors thoroughly assess the site to review and confirm compliance with building codes and industry standards.
This examination provides a comprehensive evaluation of the project’s progress and helps anticipate potential issues.
Inspections during the site phase are also essential for addressing any emerging issues promptly. By conducting regular inspections, site workers can rectify any problems before they escalate. It ensures that the project remains on track and avoids costly delays or rework.
Examination of External Factors Affecting the Construction Project
Site inspections involve evaluating external factors that may impact the construction project. These factors can range from environmental considerations to safety hazards.
Inspectors assess the site’s surroundings to identify any potential risks or constraints. This examination helps in developing strategies to mitigate risks and ensure a smooth construction process.
During the site inspection, inspectors carefully analyze the impact of nearby structures, water bodies, and other elements. Elements that may affect the project’s design and functionality.
By taking these factors into account, the construction team can make necessary adjustments and ensure the project’s longevity and quality.
Identifying Site-related Issues and Ensuring Compliance with Regulations
The site inspection phase aims to identify any site-related issues that may impact the construction project. Inspectors thoroughly examine elements such as soil conditions, drainage systems, and accessibility to ensure that the site is suitable for construction.
Additionally, site inspections are essential to ensure compliance with regulations and building codes. Inspectors verify that the construction follows all legal requirements, including zoning regulations, safety guidelines, and environmental standards.
By doing so, site inspections help prevent potential legal issues and guarantee that the construction project meets all necessary standards and regulations.
Read More on 4 Bedroom Shipping Container Home Cost – Expert Advice
Electrical Inspection
When it comes to the 4 Way Inspection process, one crucial aspect that should never be overlooked is the electrical inspection. This inspection is essential for ensuring the safety and functionality of the electrical systems within the property.
A. Importance of Electrical Inspection in 4 Way Inspection
The electrical inspection holds immense importance in the overall 4 Way Inspection process. It is conducted to assess the electrical systems thoroughly and ensure their compliance with safety standards. By doing so, it guarantees a safe and secure environment for the occupants of the property.
B. Verification of Electrical Systems and Compliance with Safety Standards
During the electrical inspection, qualified inspectors meticulously verify all electrical systems installed within the property.
This includes but is not limited to electrical wiring, panels, outlets, circuits, and fixtures. Every component is evaluated to ensure it adheres to the required safety standards and complies with building codes.
The inspection also confirms that all electrical systems are functioning efficiently and are capable of meeting the expected demand. This step is crucial as it prevents any potential hazards or malfunctions that can occur if the systems are not up to par.
C. Identification of Potential Hazards or Code Violations Related to Electrical Systems
Another key purpose of the electrical inspection is to identify any potential hazards or code violations related to the electrical systems. This includes pinpointing any faulty or unsafe wiring, incorrect installations, or overloaded circuits.
By uncovering these issues, the electrical inspection ensures that necessary actions are taken to rectify them before the property is occupied. Identifying and addressing these concerns in a timely manner not only ensures the safety of the occupants but also helps avoid any legal complications or penalties associated with code violations.
In conclusion, the electrical inspection plays a vital role in the comprehensive 4 Way Inspection process. By prioritizing electrical safety and compliance, it ensures the long-term functionality and security of the property’s electrical systems.
Read More on Shipping Container Homes in New Mexico: Expert Look
Documentation in 4 Way Inspection: The Significance and Role
Proper and thorough documentation plays a crucial role in the 4 Way Inspection process. It not only ensures compliance with regulations but also serves as a vital tool for recording findings, observations, and corrective actions throughout the inspections.
Recording Findings, Observations, and Corrective Actions
During each phase of the 4 Way Inspection, it is essential to accurately document all findings, observations, and any necessary corrective actions. This documentation provides a comprehensive record of the inspection process, allowing for easy reference and analysis.
By meticulously documenting the progress and outcomes of inspections, inconsistencies, deficiencies, or potential issues can be identified and addressed promptly.
Moreover, recording any corrective actions taken demonstrates a commitment to rectifying any matters of concern. This is to ensure the project meets all necessary standards and regulations.
Documentation as Evidence, Accountability, and Dispute Resolution
The role of documentation extends beyond the inspection phase. It serves as tangible evidence that the required inspections and compliance standards have been met throughout the construction process. In the event of disputes or claims, proper documentation becomes an invaluable resource.
Clear and comprehensive documentation offers undeniable proof of the project’s compliance. This demonstrated accountability for any actions taken or decisions made along the way. This documentation serves as a reliable reference point, minimizing the risk of discrepancies or misunderstandings during dispute resolutions.
Furthermore, having detailed records readily available can protect stakeholders and alleviate potential legal complications. Documentation acts as a reliable source of information, ensuring that any claims or disputes can be resolved efficiently and fairly.
In conclusion, proper documentation in the 4 Way Inspection process is of utmost importance. It not only facilitates accurate record-keeping but also provides evidence, accountability, and a means to resolve disputes or claims.
By meticulously documenting inspections, findings, and corrective actions, stakeholders can have peace of mind knowing they have a comprehensive record of the project’s compliance and progress.
Read More on Container Pools in NZ – Unparalleled Backyard Beauty
Safety in 4 Way Inspection
When it comes to 4 Way Inspection, safety is of paramount importance. This inspection process ensures that the structure and its occupants are in a safe environment. It involves identifying and preventing potential hazards and code violations that could compromise the safety of the building.
During the 4 Way Inspection, safety measures are taken into account to guarantee that the construction meets all necessary standards and regulations.
This includes checking the structural integrity of the building, ensuring proper installation of electrical systems, and verifying that plumbing and other essential components are in compliance with safety guidelines.
The main objective of the 4 Way Inspection is to safeguard the well-being of those who will live or work within the structure. By meticulously examining every aspect of the building’s safety, inspectors can detect any potential issues before they become major concerns.
Furthermore, a comprehensive 4 Way Inspection not only ensures the safety of the occupants but also protects the investment made in the construction project. By uncovering any safety hazards or code violations early on, necessary corrective measures can be taken, mitigating risks and potential liabilities.
Overall, safety is an integral part of the 4 Way Inspection process. It ensures that the structure complies with all safety regulations, eliminates potential dangers, and provides peace of mind for all those involved in the construction, as well as future occupants.
Read More on Are Container Homes Legal In The UK? – Taboo Homes
Handover and Occupancy
Handover and occupancy of a building are crucial steps in the construction process. These steps ensure that all necessary inspections have been conducted and that the building is safe and ready for occupation.
A. Relationship Between 4 Way Inspection and the Final Handover and Occupancy of the Building
The 4 Way Inspection plays a vital role in the final handover and occupancy of the building. This inspection ensures that all construction works.
All in all, this includes plumbing, walls, framing, electrical systems, and overall site compliance, have been completed correctly and meet the required standards.
Each aspect of the 4 Way Inspection, such as the rough inspection, site inspection, plumbing inspection, and electrical inspection, contributes to the overall assessment of the building’s readiness for occupancy. It ensures that all necessary safety measures have been implemented, and all documentation is in order.
B. Determining if the Construction is Ready for Occupation and Obtaining Certificates of Occupancy
Following a successful 4 Way Inspection, it is determined if the construction is ready for occupation. This decision is based on the inspector’s assessment of the building’s compliance with industry standards and best practices.
If the building meets all the necessary requirements, the relevant certificates of occupancy can be obtained. These certificates serve as legal documentation that signifies the building is safe for occupancy. And all necessary inspections have been performed.
Obtaining the certificates of occupancy is an essential step in the handover process. It provides assurance to the future occupants that the building has undergone thorough inspections and meets all necessary safety regulations.
Read More on Container Home Builders In Wisconsin – Affordable, Eco-friendly
C. Initiating the Next Steps of the Project After Successful Inspections
After the 4 Way Inspection and the subsequent handover and occupancy processes, the project can move on to its next stages. These stages may include the interior design, furnishing, and final preparations for the building’s use.
The successful inspections and handover also pave the way for the building to be officially opened and put to its intended purpose. This may involve advertising the availability of spaces for lease, sale, or use, depending on the nature of the building.
Industry Standards and Best Practices
A. Discussion on industry standards and best practices in 4 Way Inspection
The 4 Way Inspection process follows industry standards and best practices to ensure the highest quality in construction projects. These standards help establish a systematic approach to inspections. Above all, this ensures that all aspects of the project are thoroughly assessed for compliance and safety.
B. Importance of following established standards and guidelines
Following established standards and guidelines is crucial in the 4 Way Inspection process. It ensures that all construction activities meet the required quality and safety standards set by regulatory bodies.
By adhering to these standards, builders and contractors can avoid costly rework and delays. This results in a smoother construction process and improved customer satisfaction.
C. Achieving a high-quality final product through compliance with industry standards
Complying with industry standards during the 4 Way Inspection plays a vital role in achieving a high-quality final product. These standards cover various aspects such as structural integrity, electrical safety, plumbing compliance, and more.
Adhering to these standards helps identify any potential flaws or defects early on. Without a doubt, this allows for timely corrections and ensuring that the final product meets the highest quality standards.
Read More on Texas Container Ports in the Gulf Coast – The Powerhouse
Conclusion
Throughout this content, we have explored the crucial aspects of 4 Way Inspection in the construction industry. Let’s recap the key points covered in our discussion:
- New construction projects require various inspections to ensure compliance with safety standards and building codes.
- Inspections are carried out for different aspects of construction, including plumbing, walls, framing, electrical systems, and overall site inspection.
- Scheduled inspections are necessary to ensure that construction progresses smoothly and meets the required compliance at each stage.
- The rough inspection stage helps identify any major issues or potential problems before the construction process continues.
- Documentation plays a vital role in recording inspection results, ensuring transparency, and serving as legal proof of compliance.
- Safety should always be prioritized throughout the construction process to protect workers, occupants, and the general public.
- 4 Way Inspection signifies the final stage in the construction process. This leads to the handover of the completed project and its occupancy.
- Adhering to industry standards and best practices is essential for a successful construction project.
Reiterating the significance of 4 Way Inspection, it serves as a comprehensive evaluation of the construction project’s compliance, functionality, and safety. Neglecting this inspection can lead to serious consequences, including non-compliance penalties and potential hazards for future occupants. Therefore, it is of utmost importance to prioritize 4 Way Inspection.
Considering the complexities involved in construction projects and the importance of safety and compliance, we strongly encourage all stakeholders in the construction industry to make 4 Way Inspections an integral part of their projects.
By doing so, we can ensure the completion of safe, reliable, and regulatory-compliant constructions that meet the expectations of clients, contractors, and occupants.
Read More on Container Home Builders In Wisconsin – Affordable, Eco-friendly